In today’s highly competitive manufacturing industry, companies are constantly looking for ways to improve their processes and products. One material that has gained significant attention in recent years is SLS nylon, or selective laser sintering nylon. This additive manufacturing technology has revolutionized the way products are designed and produced, offering numerous benefits over traditional manufacturing methods. In this blog post, we will delve into the world of SLS nylon and explore its various advantages, applications, and future prospects.
What is SLS Nylon?
SLS nylon is a type of thermoplastic polymer that is created using selective laser sintering, a 3D printing process. It is also known as PA (polyamide) 12, which is the chemical name for the material. SLS nylon is made from a white powder that is heated by a high-powered laser, causing it to fuse together and form solid layers. This process is repeated layer by layer until the desired object is created.
One of the key characteristics of SLS nylon is its excellent mechanical properties. It is strong, durable, and has high impact resistance, making it suitable for a wide range of applications. Additionally, SLS nylon is lightweight, making it ideal for creating complex and intricate designs without adding unnecessary weight to the final product. Its versatility also makes it compatible with various post-processing techniques, such as dyeing, polishing, and sandblasting.
Benefits of using SLS Nylon in manufacturing
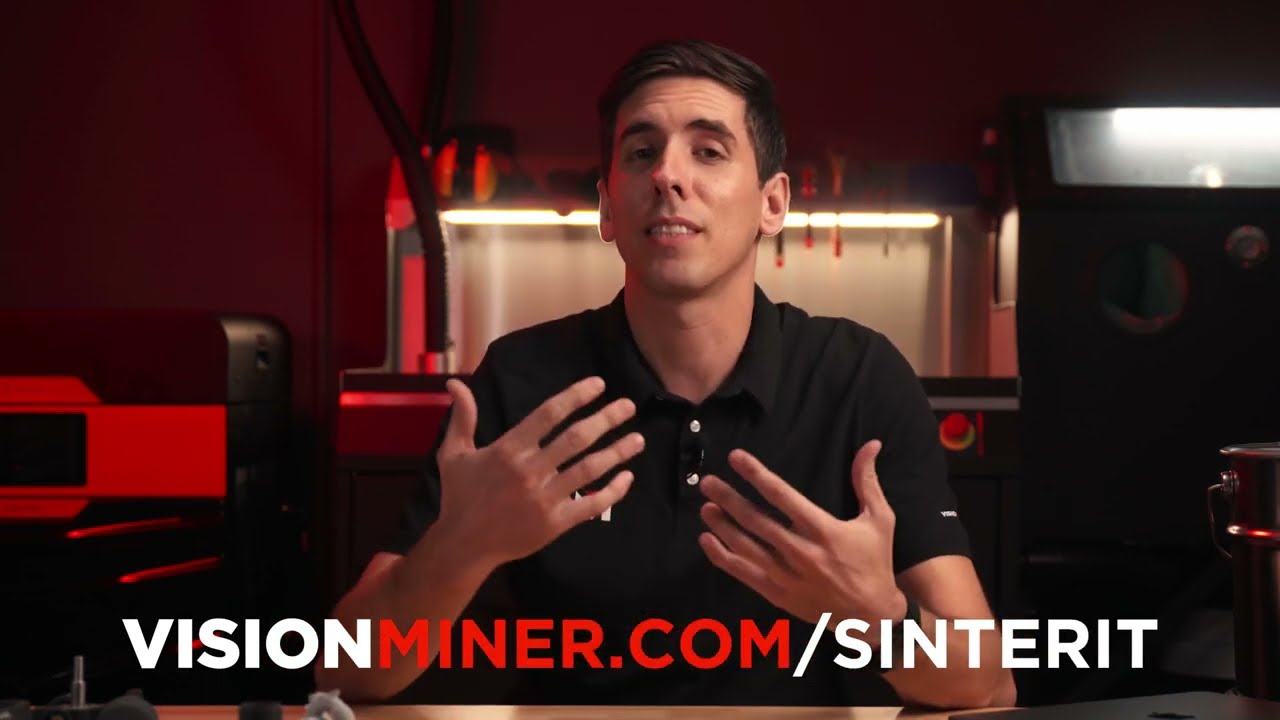
1. Design freedom and customization
One of the most significant advantages of SLS nylon is the design freedom it offers. Traditional manufacturing methods often have limitations when it comes to creating complex geometries, but with SLS nylon, almost any design can be achieved. The layer-by-layer approach allows for intricate details and undercuts to be created without the need for additional tooling, resulting in greater design flexibility. This is especially beneficial for industries such as aerospace, automotive, and medical, where customized and unique designs are crucial.
2. Cost-effective
SLS nylon is a cost-effective option for manufacturing due to its ability to create complex designs without the need for multiple parts and assembly. Traditional manufacturing methods often require the use of molds and other tooling to create intricate designs, which can be expensive and time-consuming. With SLS nylon, there is no need for these extra steps, resulting in reduced production costs and lead time.
Moreover, SLS nylon can also reduce material waste. As it is an additive manufacturing method, only the necessary amount of material is used to create the final product, minimizing excess material that would otherwise be discarded.
3. Wide range of materials
While SLS nylon is known for its excellent mechanical properties, it is not the only material that can be used with this technology. Many other materials, such as glass-filled nylon, carbon fiber-reinforced nylon, and flexible TPU, can also be sintered using the same process. This allows for even more design possibilities and opens up opportunities for creating products with different properties and characteristics.
4. Time-efficient
In today’s fast-paced world, time is of the essence. SLS nylon offers a significant advantage in terms of time efficiency compared to traditional manufacturing methods. As the process does not require any tooling, the production cycle is significantly shorter. Additionally, SLS nylon can produce multiple parts in one build, making it suitable for mass production. This means that products can be designed, produced, and brought to market much faster, giving companies a competitive edge.
5. Reduced risk of errors
With traditional manufacturing methods, human error is always a possibility. However, with SLS nylon, the entire production process is automated, minimizing the risk of errors. This results in consistent and accurate production, ensuring that products are of the highest quality and meet all specifications. Moreover, as SLS nylon is a digital process, the design can be digitally modified and tested before being sent for production, reducing the risk of errors even further.
Applications of SLS Nylon in modern manufacturing
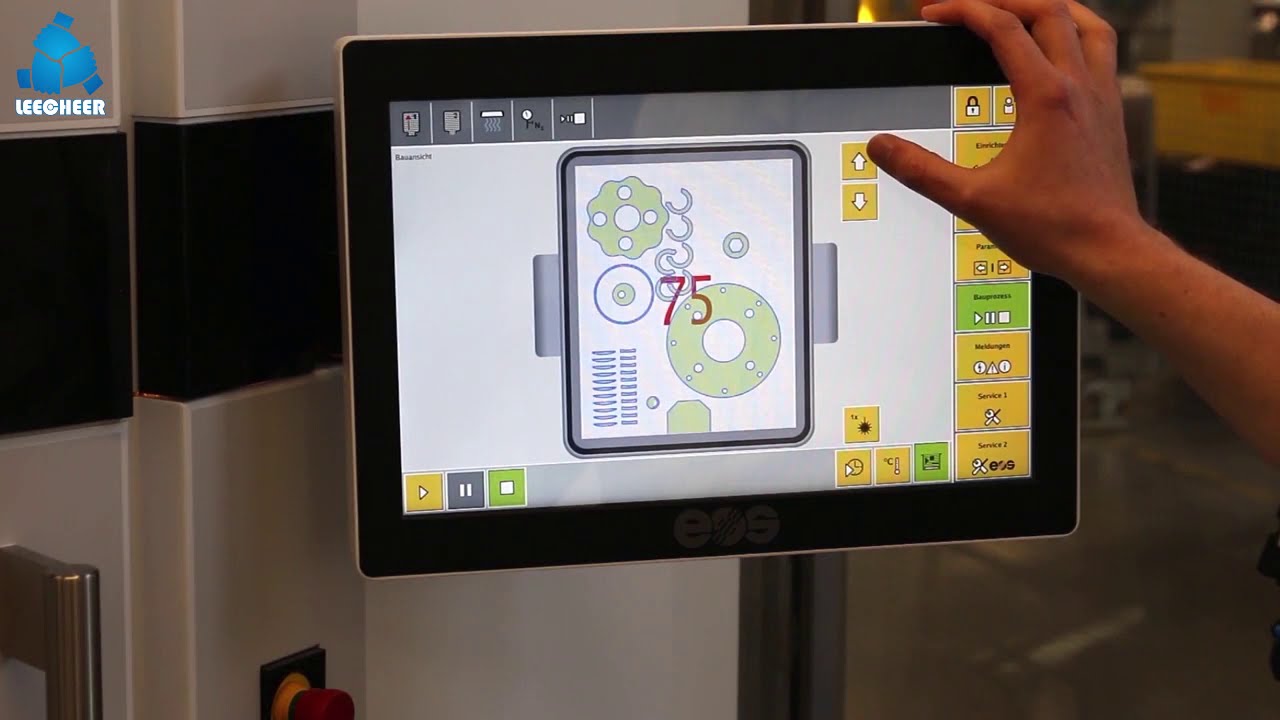
SLS nylon has found its way into a wide range of industries and applications, thanks to its numerous benefits and versatility. Here are some of the most common applications of SLS nylon in modern manufacturing:
1. Aerospace
The aerospace industry has been one of the early adopters of SLS nylon. The lightweight yet strong properties of SLS nylon make it ideal for creating parts for aircraft and spacecraft. Additionally, as the technology offers design freedom, complex and intricate designs required in the aerospace industry can be achieved with ease. Furthermore, SLS nylon’s ability to withstand high temperatures and exposure to chemicals makes it suitable for use in engines and other critical components.
2. Automotive
Similar to the aerospace industry, the automotive industry also values SLS nylon for its lightweight and strong properties. It is widely used in the production of interior and exterior parts, such as dashboards, door panels, and bumpers. Additionally, the customization possibilities offered by SLS nylon make it a popular choice for creating personalized car accessories.
3. Medical and healthcare
SLS nylon has also made significant contributions to the medical and healthcare industry. Its biocompatibility and sterilizability make it suitable for creating medical devices and implants. With the ability to create customized designs based on patient-specific data, SLS nylon has revolutionized the medical field, allowing for better patient outcomes.
4. Consumer goods
From household appliances to electronic devices, SLS nylon has become an integral part of the consumer goods industry. Its design flexibility and cost-effectiveness have made it a popular choice for creating unique and functional products. SLS nylon is also used in the production of sports equipment, such as helmets and bicycle frames, due to its lightweight and durable properties.
5. Industrial and tooling applications
SLS nylon has also found its way into industrial and tooling applications. Its high strength and durability make it suitable for creating tools and jigs for manufacturing processes. The ability to create complex designs also makes it ideal for creating molds for injection molding and other processes.
Comparison with other manufacturing materials
While SLS nylon offers numerous benefits, it is essential to compare it with other manufacturing materials to understand its full potential.
1. SLS nylon vs. traditional plastics
Traditional plastics, such as ABS and polycarbonate, have been widely used in manufacturing for decades. However, they are often limited in terms of design flexibility and require additional post-processing steps, such as machining and assembly. On the other hand, SLS nylon can achieve intricate designs without the need for multiple parts and post-processing. It also has better mechanical properties and can withstand higher temperatures, making it a more versatile option.
2. SLS nylon vs. metal
Metal is the traditional go-to material for industries such as aerospace and automotive due to its strength and durability. However, SLS nylon offers comparable properties to some metals, such as aluminum, at a fraction of the weight. This makes it an attractive alternative for creating lightweight components without compromising on strength. Additionally, the cost-effectiveness and design flexibility of SLS nylon make it a more attractive option for certain applications.
3. SLS nylon vs. other additive manufacturing technologies
SLS nylon is not the only additive manufacturing technology available in the market. Other methods, such as FDM and SLA, also offer similar benefits. However, SLS nylon has an advantage over these technologies in terms of material properties. It produces parts with better mechanical properties and is compatible with a wider range of materials, including high-performance polymers.
Case studies or examples of successful use
1. NASA’s Mars Rover Wheels
In 2019, NASA’s Mars Rover wheels were redesigned using SLS nylon after the original aluminum wheels suffered significant damage. The new wheels, called Superelastic Tires, are made from a composite material consisting of SLS nylon and titanium springs. This design has proved to be more durable and lightweight, allowing the rover to move across rough terrain with ease.
2. Adidas Futurecraft 4D shoes
Adidas has been incorporating 3D printing and additive manufacturing into their footwear for several years now. In collaboration with Carbon, they have created the Futurecraft 4D shoes, which feature an SLS nylon midsole. This allows for customized cushioning and support based on the wearer’s data, resulting in comfortable and high-performance shoes.
Future prospects and trends in SLS Nylon manufacturing industry
SLS nylon is still a relatively new technology, and there is much room for growth and innovation. Some of the trends and future prospects in the SLS nylon manufacturing industry include:
- Advancements in material properties: Researchers and scientists are constantly working on improving the mechanical and chemical properties of SLS nylon. This will open up new possibilities for its use in different industries and applications.
- Increased adoption in the medical field: As SLS nylon offers biocompatibility and customization options, it is expected to see increased use in the medical field for creating implants and prosthetics.
- Integration with Industry 4.0: With the rise of Industry 4.0, it is expected that SLS nylon will become more integrated with other technologies such as AI and IoT. This will lead to better quality control, production optimization, and cost reduction.
Conclusion
SLS nylon has undoubtedly changed the game in modern manufacturing. Its numerous benefits, such as design freedom, cost-effectiveness, and time-efficiency, make it a valuable tool for businesses looking to improve their processes and products. With its wide range of applications, compatibility with various materials, and potential for future advancements, SLS nylon is set to play an even more significant role in the manufacturing industry in the years to come.