With the constant advancement in technology, the manufacturing industry has also undergone a significant transformation. Traditional methods of manufacturing are slowly being replaced by innovative and efficient techniques such as 3D printing. Among the various types of 3D printing technology, selective laser sintering (SLS) is gaining popularity due to its ability to produce high-quality, complex designs at a faster rate. In this blog post, we will dive into the world of SLS 3D printing technology and explore its impact on the manufacturing sector.
Benefits of SLS 3D Printing in Manufacturing
Cost-Efficiency
One of the main advantages of using SLS 3D printing technology in manufacturing is its cost-efficiency. Unlike traditional manufacturing methods, SLS does not require expensive molds or tooling, which can significantly reduce production costs. Additionally, multiple parts can be printed simultaneously, making it a more time and cost-effective option for mass production.
Moreover, SLS allows for the use of a wide range of materials such as nylon, polycarbonate, and even metal powders, depending on the specific needs of the project. This versatility eliminates the need for purchasing different types of machines for different materials, further reducing costs.
Complex Designs and Customization
Traditional manufacturing methods often have limitations when it comes to producing intricate designs. However, with SLS 3D printing, even the most complex designs can be produced with ease. The layer-by-layer printing process allows for the creation of detailed and precise geometries that would be impossible to achieve through traditional methods.
Furthermore, SLS 3D printing enables customization on a whole new level. With the ability to print unique designs for each product, companies can cater to individual customer demands and preferences, resulting in higher customer satisfaction.
Reduced Waste and Environmental Impact
Another significant benefit of SLS 3D printing in manufacturing is the reduction of waste and its positive impact on the environment. Traditional methods often result in excess material being discarded, leading to higher production costs and environmental pollution.
SLS 3D printing uses only the necessary amount of material for each project, minimizing waste and reducing the carbon footprint. Moreover, the materials used in SLS 3D printing are recyclable, making it a more sustainable option for manufacturing.
Fast Production Times
In today’s fast-paced world, time is of the essence, and SLS 3D printing offers a solution for that. With traditional manufacturing methods, the process can take weeks or even months, depending on the complexity of the design. SLS 3D printing, on the other hand, can produce parts within hours, drastically reducing production times.
This speed of production allows for faster product development and testing, enabling companies to bring their products to market at a much faster rate. This advantage is particularly beneficial for industries such as aerospace and automotive, where timely production is crucial.
Applications of SLS 3D Printing in Various Industries
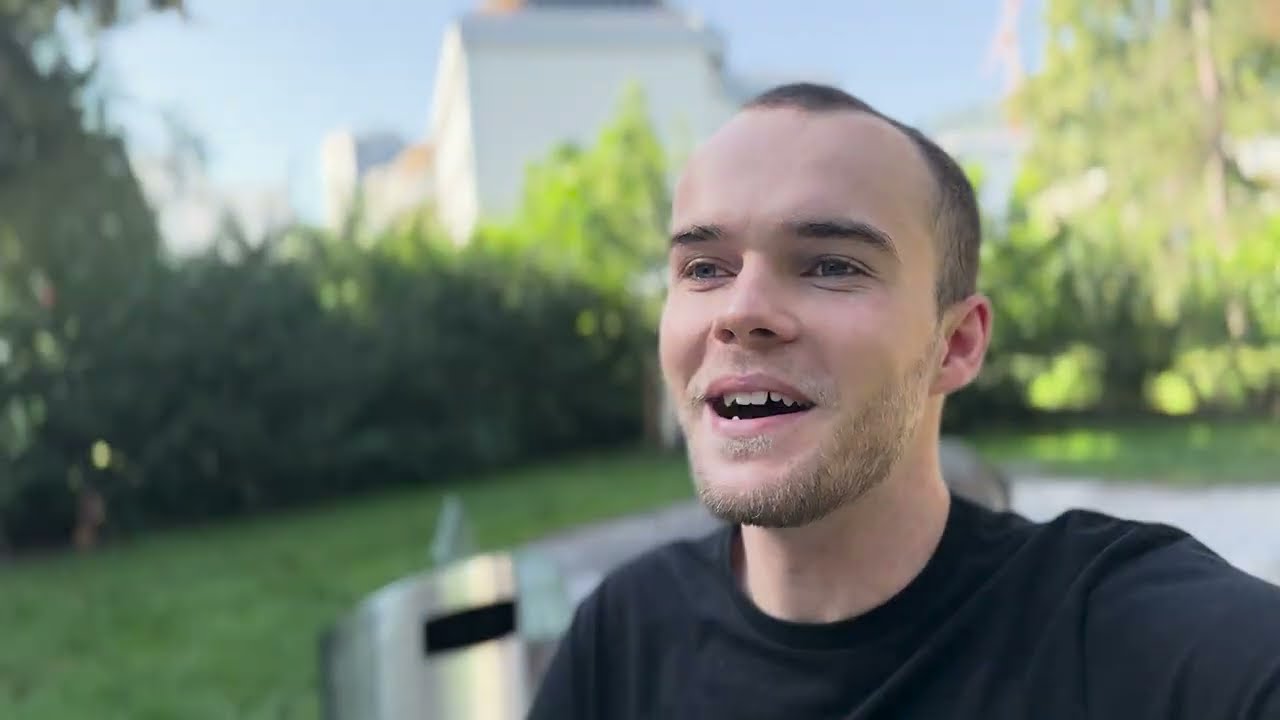
SLS 3D printing has found applications in various industries, revolutionizing the way products are designed, produced, and delivered. Let’s take a look at some of the industries where SLS 3D printing is making an impact:
Aerospace and Defense
The aerospace and defense industry demands high-quality, lightweight, and durable parts for their equipment. SLS 3D printing technology allows for the production of complex designs with minimal weight, making it ideal for these industries.
Moreover, SLS 3D printing enables the creation of customized parts and tools, which are often needed in the aerospace and defense sector. This reduces lead times and production costs while also improving the overall performance of the equipment.
Automotive
The automotive industry has been utilizing SLS 3D printing to produce prototypes, spare parts, and even functional components. With the ability to print complex and lightweight designs, SLS has enabled the production of more efficient and fuel-efficient vehicles.
Additionally, SLS technology allows for on-demand manufacturing, enabling companies to quickly produce parts as needed, reducing inventory costs and waste.
Medical and Healthcare
SLS 3D printing has also found applications in the medical and healthcare sector, particularly in the production of prosthetics, implants, and surgical tools. The ability to create customized designs based on a patient’s specific needs has greatly improved the success rates of surgeries and treatments.
Moreover, with SLS, medical devices can be produced with biocompatible materials, ensuring safety and compatibility with the human body. This has opened up new possibilities for personalized medicine and revolutionized the healthcare industry.
Consumer Goods
The consumer goods industry has also embraced SLS 3D printing technology to produce unique and customized products. From household items to fashion accessories, SLS enables designers to bring their visions to life without the limitations of traditional manufacturing methods.
Furthermore, with the increasing demand for sustainable and eco-friendly products, SLS 3D printing offers a viable solution by reducing waste and using recyclable materials.
Case Studies of Successful Implementation
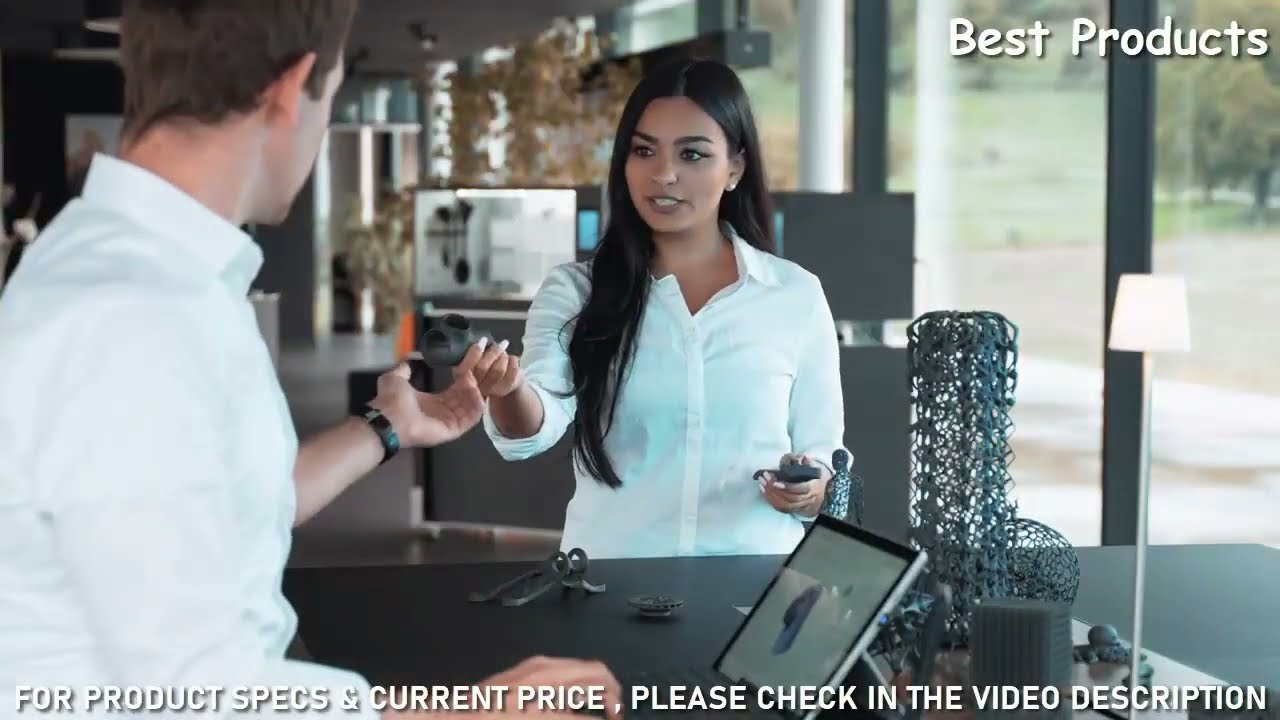
BMW
German automaker BMW has been utilizing SLS 3D printing technology in its production processes since 2010. With the goal of creating lighter, stronger, and more efficient vehicles, BMW has used SLS to produce components such as air intake manifolds and water pumps.
By implementing SLS, BMW has been able to reduce production times significantly, improve the performance of their vehicles, and reduce material waste. This has resulted in cost savings and an increase in overall efficiency.
Johnson & Johnson
Pharmaceutical giant Johnson & Johnson has incorporated SLS 3D printing into its production processes for medical devices and equipment. With the ability to produce custom-made designs, Johnson & Johnson has been able to improve patient outcomes and reduce the risk of infection.
Moreover, SLS allows for the production of complex designs with bio-compatible materials, ensuring safety and compatibility with the human body. This has enabled Johnson & Johnson to develop innovative medical solutions while also reducing production costs.
Adidas
Sportswear company Adidas has embraced SLS 3D printing technology to produce customized sports shoes for professional athletes. By using SLS, Adidas can create unique designs that cater to each athlete’s specific needs, improving their performance on the field or court.
SLS also allows for the production of lightweight and flexible designs, providing athletes with maximum comfort and support. This has given Adidas a competitive edge in the market and has attracted a loyal customer base.
Future Potential and Growth of SLS 3D Printing in Manufacturing Sector
The demand for SLS 3D printing technology is expected to grow exponentially in the coming years. According to a report by MarketsandMarkets, the global SLS 3D printing market is projected to reach $3.7 billion by 2024, growing at a CAGR of 27.5% from 2019 to 2024.
This growth can be attributed to the increasing adoption of 3D printing technology in various industries, advancements in SLS materials, and the development of high-speed SLS machines. As more companies realize the benefits of SLS, we can expect to see a significant shift towards this technology in the manufacturing sector.
Moreover, as 3D printing technology continues to evolve, we can expect to see even more versatile and cost-effective SLS options in the future. This will open up new possibilities for custom-made products and personalized manufacturing, further driving the growth of SLS 3D printing.
Conclusion
SLS 3D printing technology has revolutionized the manufacturing industry, offering numerous benefits such as cost-efficiency, complex designs, reduced waste, and fast production times. Its applications in various industries have showcased its versatility and potential for growth.
As the demand for SLS 3D printing continues to rise, we can expect to see even more advancements in this technology, leading to further improvements in manufacturing processes and products. By embracing SLS, companies can stay ahead of the competition and cater to the ever-growing demands of customers in a constantly evolving market.