The world of manufacturing has seen tremendous advancements in recent years, especially with the introduction of 3D printing technology. Among the various types of 3D printing methods, Selective Laser Sintering (SLS) has emerged as a game-changing technique for producing high-quality, complex, and functional parts. SLS 3D printing technology has revolutionized the way products are designed, developed, and manufactured, making it one of the most sought-after techniques in the manufacturing sector.
SLS 3D printing technology involves using a laser to fuse small particles of material together to create a three-dimensional object layer by layer. It uses a powdered material, such as nylon or metal, which is melted and solidified by a laser to form the desired shape. This process allows for the creation of intricate and precise designs that were previously impossible to achieve with traditional manufacturing methods. In this blog post, we will explore the benefits, applications, case studies, and future potential of SLS 3D printing in the manufacturing industry.
Benefits of SLS 3D Printing in Manufacturing
Cost-Effective Production
One of the main advantages of SLS 3D printing in manufacturing is its cost-effectiveness. Unlike traditional manufacturing methods that require expensive molds or tooling, SLS 3D printing does not have any upfront costs associated with creating molds. This greatly reduces the production costs, especially for small batch productions. Additionally, SLS 3D printing allows for the use of multiple materials in a single print, further reducing production costs and increasing efficiency.
Complex and Customizable Designs
With SLS 3D printing, intricate and complex designs can be easily created. This is due to the layer-by-layer manufacturing process, which allows for the creation of shapes and geometries that cannot be achieved through traditional manufacturing methods. This opens up endless possibilities for product customization, allowing manufacturers to cater to the specific needs and requirements of their customers.
Fast Turnaround Time
SLS 3D printing technology offers a much faster turnaround time compared to traditional manufacturing methods. The entire process, from design to production, can be completed in a matter of hours or days, depending on the complexity of the design. This makes it an ideal choice for rapid prototyping, where quick iterations and modifications are necessary.
Reduced Waste and Environmental Impact
SLS 3D printing is an additive manufacturing process, meaning that material is only added where it is needed, rather than subtracted like in traditional methods. This leads to significantly less material waste, making it a more environmentally friendly option. Additionally, SLS 3D printing uses powdered materials, which can be recycled and reused, further reducing its impact on the environment.
High-Quality and Functional Parts
SLS 3D printing technology produces high-quality and functional parts that can withstand rigorous testing and real-world use. This is due to the strength and durability of the materials used, such as nylon, which is commonly used in SLS 3D printing. The parts produced through this method have excellent mechanical properties and can meet the requirements of various industries, including aerospace, automotive, and medical.
Applications of SLS 3D Printing in Various Industries
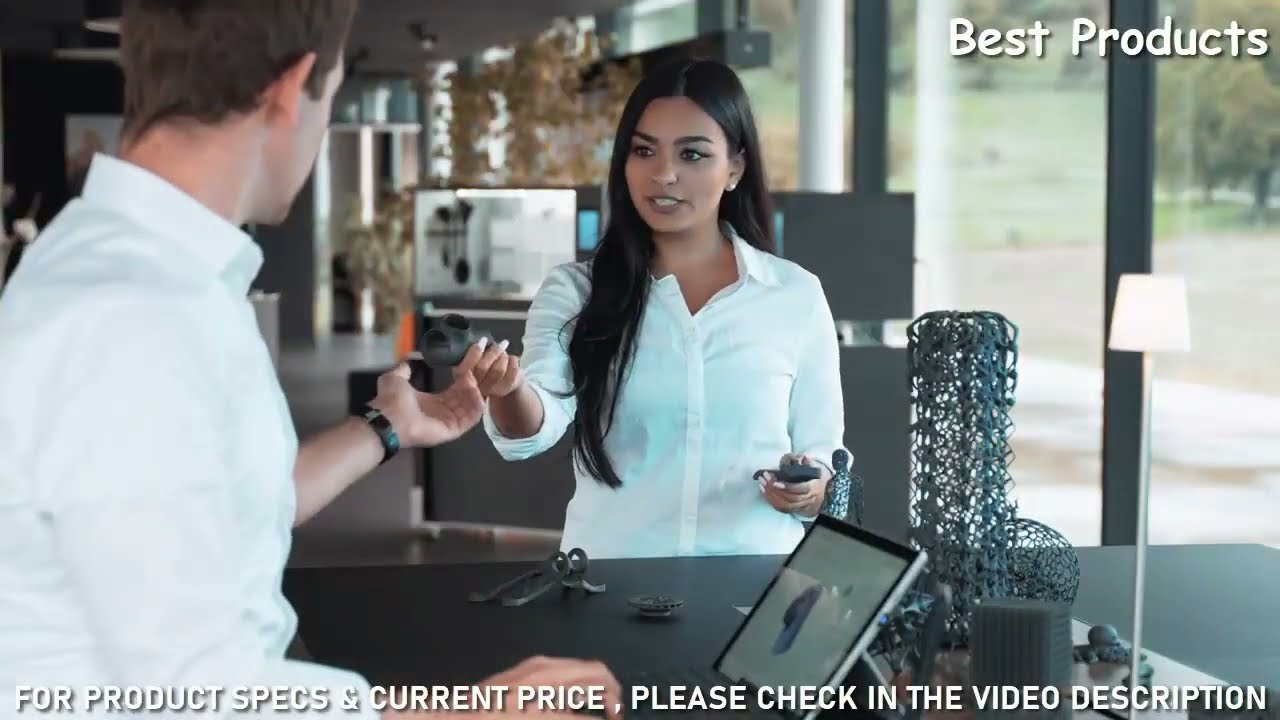
Aerospace Industry
The aerospace industry has been one of the early adopters of SLS 3D printing technology. The ability to produce complex and lightweight parts with high strength and durability makes SLS 3D printing a perfect fit for this industry. SLS 3D printed parts have been used in aircraft engines, interior components, and even entire rocket engines. This has not only reduced the weight of the parts but also reduced the overall production time and costs.
Automotive Industry
Similar to the aerospace industry, the automotive sector has also embraced SLS 3D printing for its ability to produce lightweight and high-strength parts. This has been particularly useful in the production of electric vehicles, where weight reduction is crucial for increasing their driving range. Additionally, SLS 3D printing allows for the creation of customized designs and low-volume production, making it a cost-effective solution for prototyping and small-scale manufacturing.
Medical Industry
The medical industry has also benefited greatly from SLS 3D printing technology. The ability to create customized and patient-specific implants and prosthetics has revolutionized the field of medicine. With SLS 3D printing, complex designs can be created that perfectly fit a patient’s anatomy, reducing the need for multiple surgeries and improving the overall success rate. Additionally, SLS 3D printing has allowed for the production of advanced medical devices, such as artificial joints, that are stronger and more durable than traditional options.
Consumer Goods Industry
SLS 3D printing has also made an impact in the consumer goods industry, where customization and quick turnaround time are essential. Many companies have started using SLS 3D printing to produce prototypes and small-batch products, allowing them to bring new products to market faster and at a lower cost. This has also opened up opportunities for customizable and scalable production, where customers can personalize products according to their preferences.
Other Industries
Apart from the above-mentioned industries, SLS 3D printing has found applications in various other sectors, including defense, architecture, and jewelry. In the defense sector, SLS 3D printing has been used to produce lightweight and durable components for military equipment. In architecture, it has been used to create intricate models and prototypes for building designs. In the fashion industry, SLS 3D printing has been used to produce unique and customizable jewelry pieces, showcasing the potential of this technology in creative fields.
Case Studies of Successful Implementation
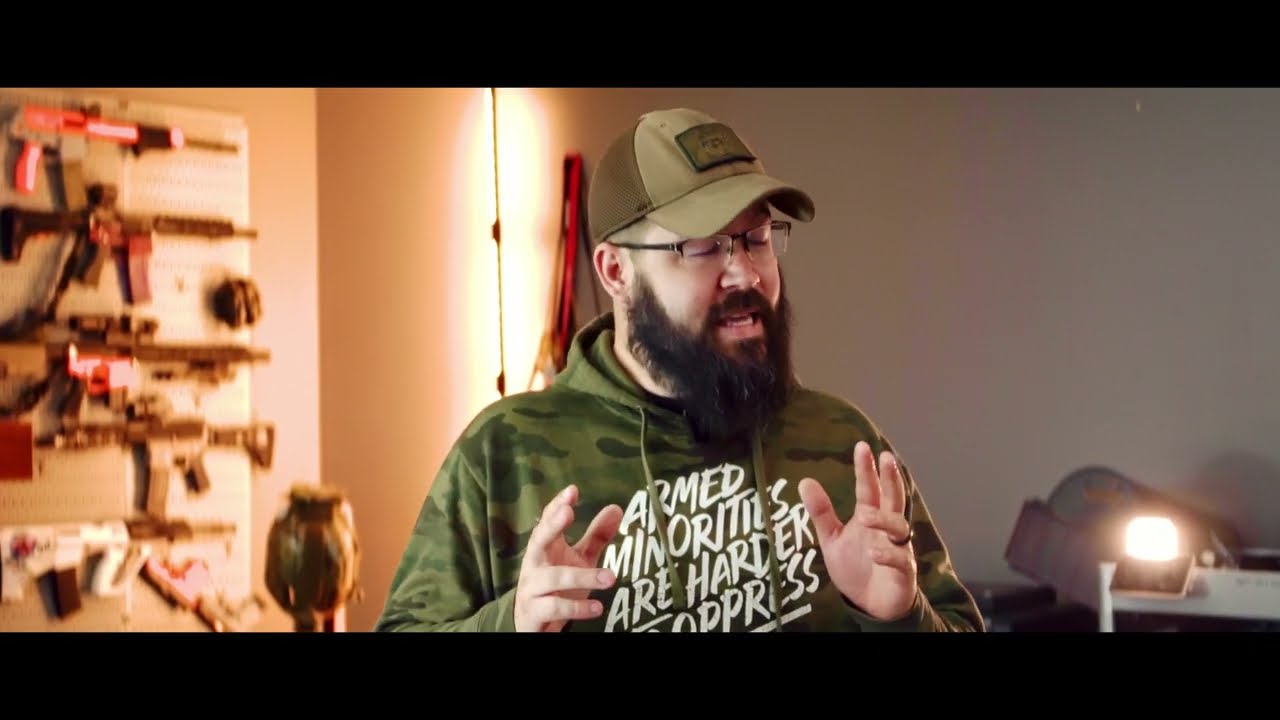
GE Aviation
GE Aviation, one of the world’s largest aircraft engine manufacturers, has heavily invested in SLS 3D printing technology. They have utilized this technology to produce complex fuel nozzles for their LEAP engines, which are used in planes such as the Boeing 737 MAX and Airbus A320neo. The use of SLS 3D printing has reduced the weight of these parts by 25%, increased their durability, and reduced their production time from months to weeks.
Adidas
Adidas, a leading sports apparel company, has also incorporated SLS 3D printing into their manufacturing process. They have used this technology to produce midsole components for their Futurecraft 4D shoes. The midsoles are designed using data from an individual’s foot scan, providing a customized and comfortable fit. With SLS 3D printing, Adidas can mass-produce these customized shoes at a much faster rate than with traditional methods.
Align Technology
Align Technology, the company behind the popular Invisalign clear aligners, has leveraged SLS 3D printing to revolutionize the orthodontic industry. By using SLS 3D printing to produce patient-specific aligners, they have been able to reduce the treatment time and improve the accuracy of the aligners. This has made the process more efficient and effective, resulting in higher customer satisfaction rates.
Future Potential and Growth of SLS 3D Printing in Manufacturing sector
SLS 3D printing technology is still in its early stages, and there is immense potential for growth and development in the manufacturing sector. As the technology continues to advance, we can expect to see even more complex and functional products being produced through SLS 3D printing. Some of the potential future developments include:
- Use of new materials: Currently, SLS 3D printing mainly uses nylon and metal powders. However, research is underway to develop new materials that can be used in this process. This will open up new possibilities for the type of products that can be produced through SLS 3D printing.
- Increase in production speed: With advancements in technology, we can expect to see an increase in the production speed of SLS 3D printing. This will lead to even faster turnaround times and increased efficiency in the manufacturing process.
- Integration with other technologies: SLS 3D printing has the potential to be integrated with other technologies like artificial intelligence and robotics. This can further automate the manufacturing process and reduce human involvement, making it more efficient and cost-effective.
- Expansion into new industries: As SLS 3D printing continues to evolve, we can expect to see its adoption in new industries that have not yet explored its capabilities. This could result in innovations in fields such as food, electronics, and construction, among others.
Conclusion
SLS 3D printing technology has made a significant impact on the manufacturing sector, and its potential for growth and development is immense. From producing complex and customized products to reducing costs and environmental impact, this technology offers numerous benefits to manufacturers. With continuous advancements and research in this field, we can only expect to see even greater achievements from SLS 3D printing in the future. It truly is revolutionizing the way products are designed, developed, and manufactured, and its impact will only continue to grow in the coming years.